A205 Cardboard & Plastic Baler
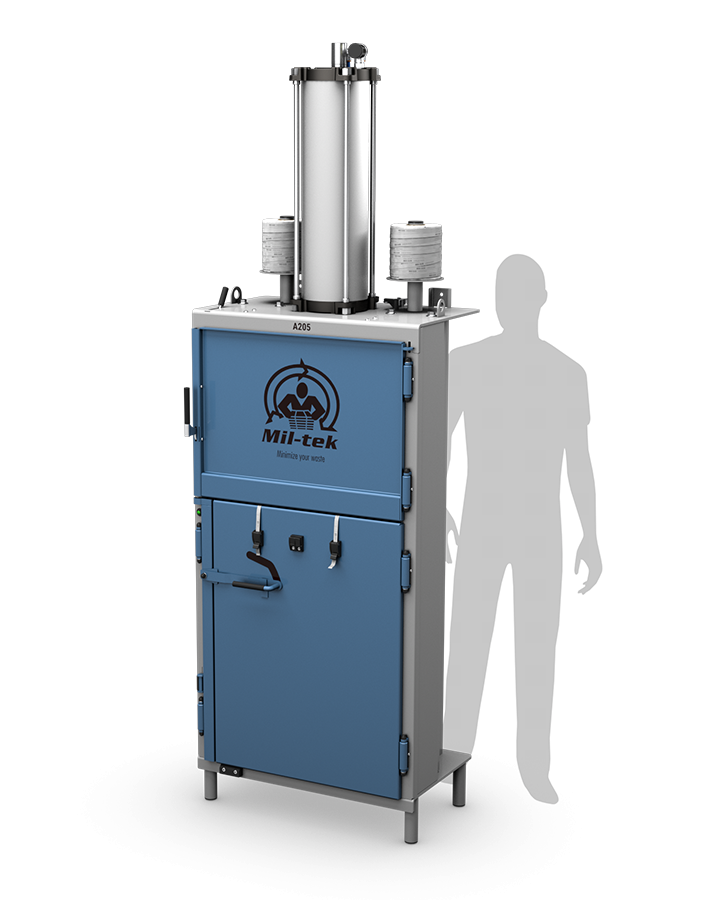
The A205 is our fastest and most versatile baler, combining innovative pneumatic technology with a small physical footprint.
- Bale 50 kg cardboard & 120 kg plastic
- Double-acting cylinder with ECODrive
- Floorspace footprint of just 0.45m²
- Worlds’ fastest pressing cycle
- Optimal working height
- EN16500 certified
- Bale size is adjustable