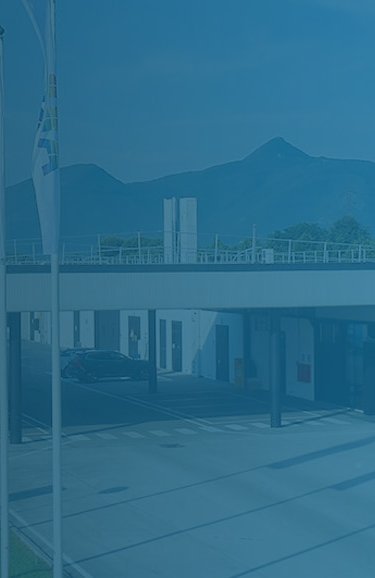
ABB started using lean manufacturing techniques to maximise waste management
– Leading to the highest ranking of the UL2799A Zero Waste to Landfill Validation!
The ABB Frosinone facility in Italy obtained the highest validation possible of the UL 2799A Environmental Claim Validation Procedure for Zero Waste Classifications following Mil-tek’s adjustments to the company’s waste handling.
One of several outcomes of the changes was an 80% decrease in internal forklift usage!
0%
Highest rated Zero Waste to Landfill Validation
ABB provides solutions that optimise the creation, movement, powering, and use of objects by fusing software and engineering know-how. This sets the stage for a future where resources are used more wisely and sustainably.
However, adjustments had to be made to the way waste was handled at the Italian ABB Frosinone factory. So they joined forces with Mil-tek!
As a consequence of our collaboration, the UL 2799A Environmental Claim Validation Procedure for Zero Waste Classifications has validated the platinum rating. To be awarded the highest “platinum” rating, a facility needs to demonstrate that it routinely achieves a 100% diversion rate of landfill waste.
Let’s examine how we got there…
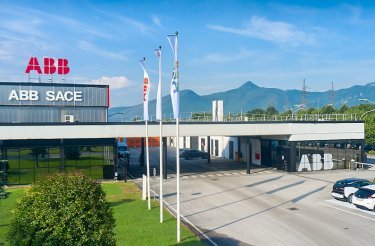
Equipment for compacting, handling optimisation, and Lean processes
Mil-tek carried out extensive workflow mapping to watch the operator movements and manufacturing operations at the Frosinone factory. Following the assessment, Mil-tek compacting equipment and leaner handling processes were implemented in ABB’s production.
The workflow mapping revealed how forklifts at the facility that handled waste logistics was travelling an average of about 11,000 km annually! After the implementation of Mil-tek balers and Lean optimization, the average distance travelled by forklifts was reduced by 80% to 2,200 km.
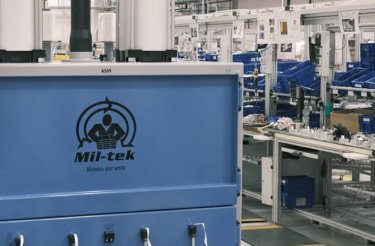
Overall benefits for ABB
Mil-tek installed a range of pneumatic balers in the factory. Since air lines were already in place at the factory, the machines were installed directly on the production line to maximise efficiency.
Here, they compact and reduce cardboard and plastic waste volumes, and cut the frequency of visits to outside containers by up to 90%.
Further benefits for ABB:
– leaner waste handling
– more streamlined workflow
– an 80% decrease in forklift truck use
– a significant decrease in accident risk
– a reduction in the number of outdoor containers
– time freed up for more important activities
– and more

Have a question?
Get in touch with us right now to find out how improved waste management from Mil-tek may help your business save time, space, and money.